Magnesium alloy series——Magnesium-zirconium master alloy
I. The role of zirconium in magnesium alloys
Fine grain strengthening is one of the most effective methods of strengthening magnesium alloys to enhance their strength, improve plasticity and toughness. At present, the most commonly used methods of fine-crystal strengthening is metal alloying, that is, by adding single elements and compounds to the alloy particles to refine the magnesium alloy, such as Zr, Ca, Si and other grain growth inhibition factor GRF (Growth Restriction Factor) value of the larger elements. Among them, the GRF value of Zr element is 38.29, and the crystal structure is highly similar to that of Mg, which has the most significant effect on the refinement of Mg-RE alloys. At the same time, the addition of Zr can reduce the tendency of the alloy to thermal cracking, and improve the strength, plasticity and creep resistance. However, there is a huge difference in the properties of Zr and Mg elements, as shown in Table 1; and the two elements are basically immiscible, as shown in the binary phase diagram of Mg-Zr in Fig. 1. Numerous studies have shown that the best way to add Zr is through the addition of Mg-Zr master alloy in molten magnesium.
Table 1 Comparison of the properties of Zr and Mg
Elements | Mg | Zr |
Melting Point/℃ | 650 | 1855 |
Boiling Point/℃ | 1107 | 4409 |
Density/g▪cm-3 | 1.738 | 6.51 |
Crystalline Structure | hcp | hcp |
Lattice Constant | a = 0.32092 nmc = 0.52105 nmc/a = 1.6236 | a = 0.3232 nmc = 0.5147 nmc/a = 1.5925 |
Atomic Radius/nm | 0.162 | 0.16 |
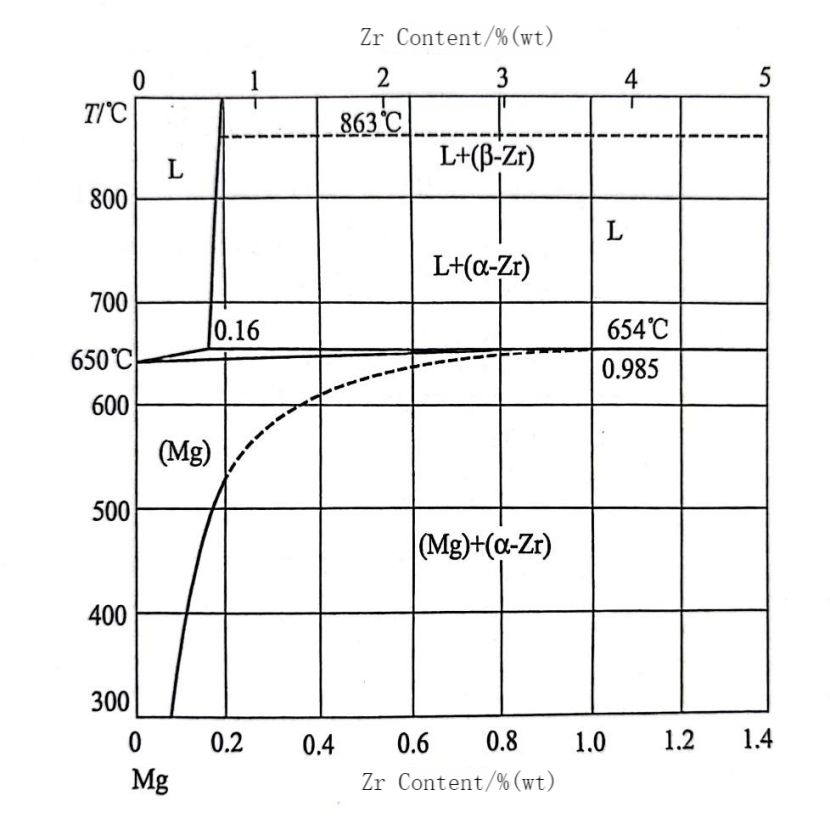
Figure 1 Mg-Zr binary phase diagram
II. Magnesium-zirconium master alloy preparation process
The traditional preparation process of Mg-Zr master alloy is the magnesium thermal reduction method, which is, by covering with molten salt for protection, at a high temperature above 1100℃, through mechanical stirring, the excess metal Mg reacts with potassium zirconium fluoride in excess to undergo reduction reaction, thereby reducing out metal Zr particles, and then forming Mg-Zr master alloy with the excess metal Mg. The reduction temperature of this process is much higher than the melting point of metal Mg, which will inevitably lead to the oxidation and combustion of metal Mg to produce a large amount of smoke; on the other hand, due to the use of potassium zirconium fluoride as raw material, and take the molten salt cover protection mode, it will definitely produce a large number of fluorine-containing waste residue, and the environment is very serious pollution. And the Mg-Zr master alloy prepared by this process has a series of quality problems such as compositional segregation, coarse zirconium particles, agglomeration, easy oxidation corrosion, etc., which can’t meet the quality and performance requirements of the new generation of high-performance rare earth magnesium alloys.
Our company has independently developed a new process of preparing high quality Mg-Zr master alloy by non-magnesium thermal reduction method. The process adopts unique melting and stirring technology that through the gas protection mode, the melting temperature can be controlled below 700 ℃, not only the production environment is friendly and pollution-free, suitable for large-scale production, and the resulting Mg-Zr master alloy in the Zr particles of fine size, uniform distribution, no large particles of agglomeration, non-oxidizing corrosion, and the use of the process of high yield. The products are shown in Figure 2.
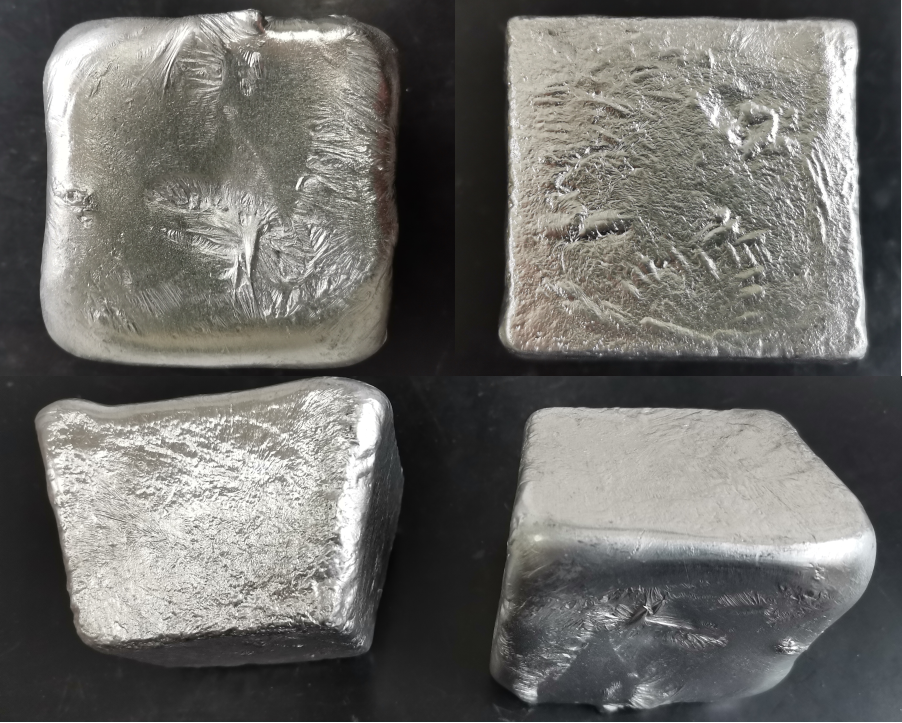
Figure 2 Mg-Zr master alloy
III. Magnesium-zirconium master alloy technical indicators
1. Composition
Table 2 Mg-Zr master alloy composition table
Type | Specification | Impurity content | Remark |
Mg-Zr10 | Zr:10±1% | Fe≤0.02%、Si≤0.02%、Mn≤0.02%、Ca≤0.02%、Ni≤0.002%、Al≤0.007%、Cu≤0.0008% | Zr content can be customized upon request |
Mg-Zr20 | Zr:20±2% | ||
Mg-Zr30 | Zr:30±2% |
2. Microstructure and Zr particle size
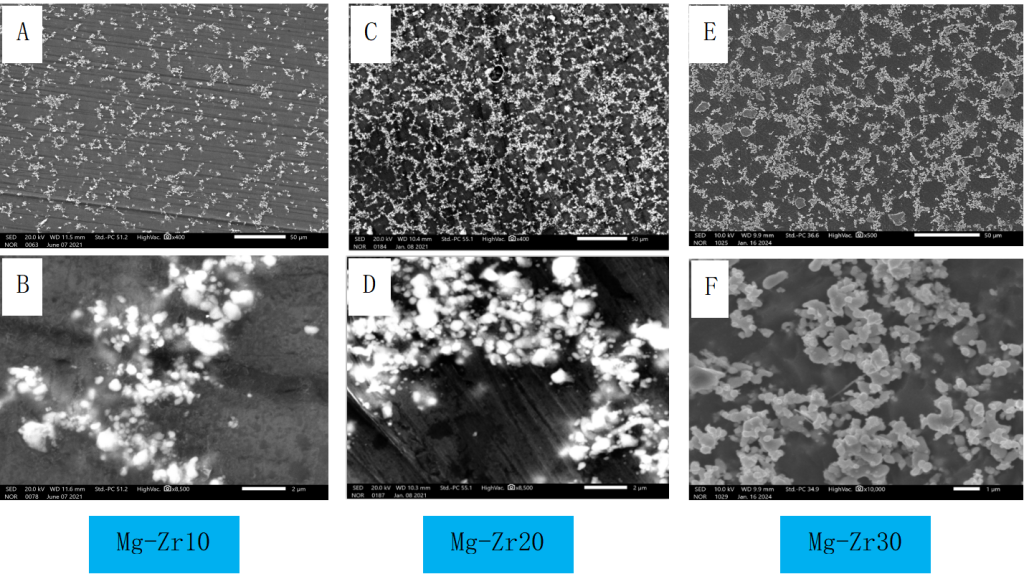
Figure 3 microstructure of different Zr content Mg-Zr master alloy
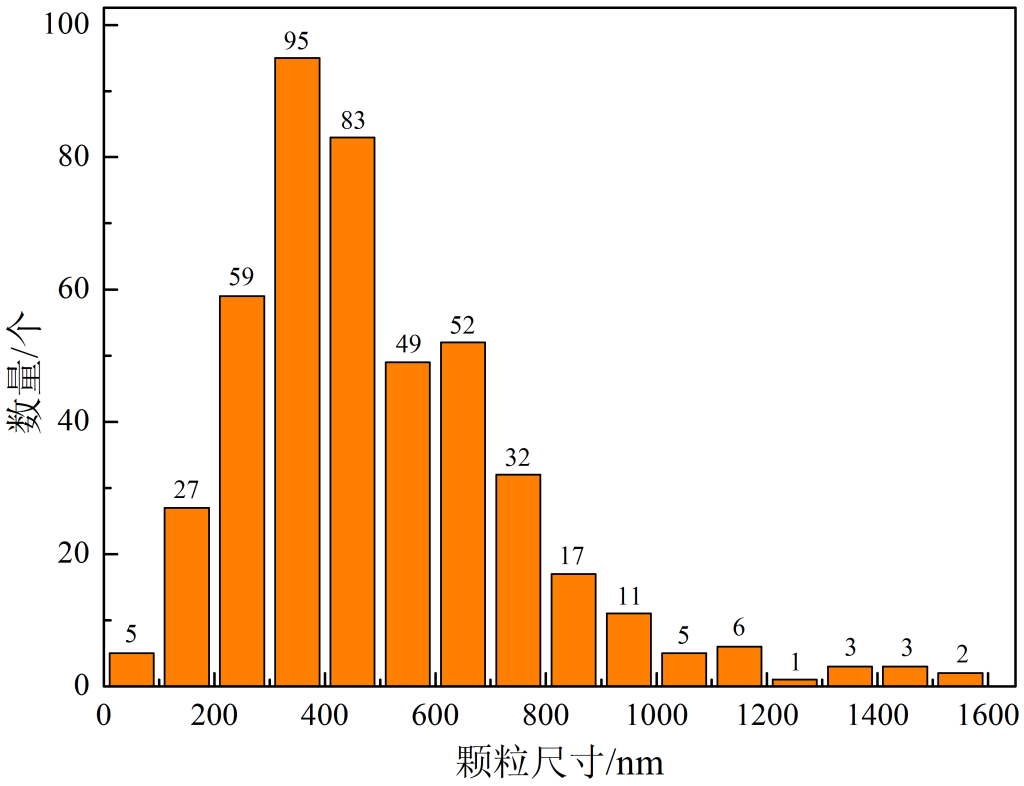
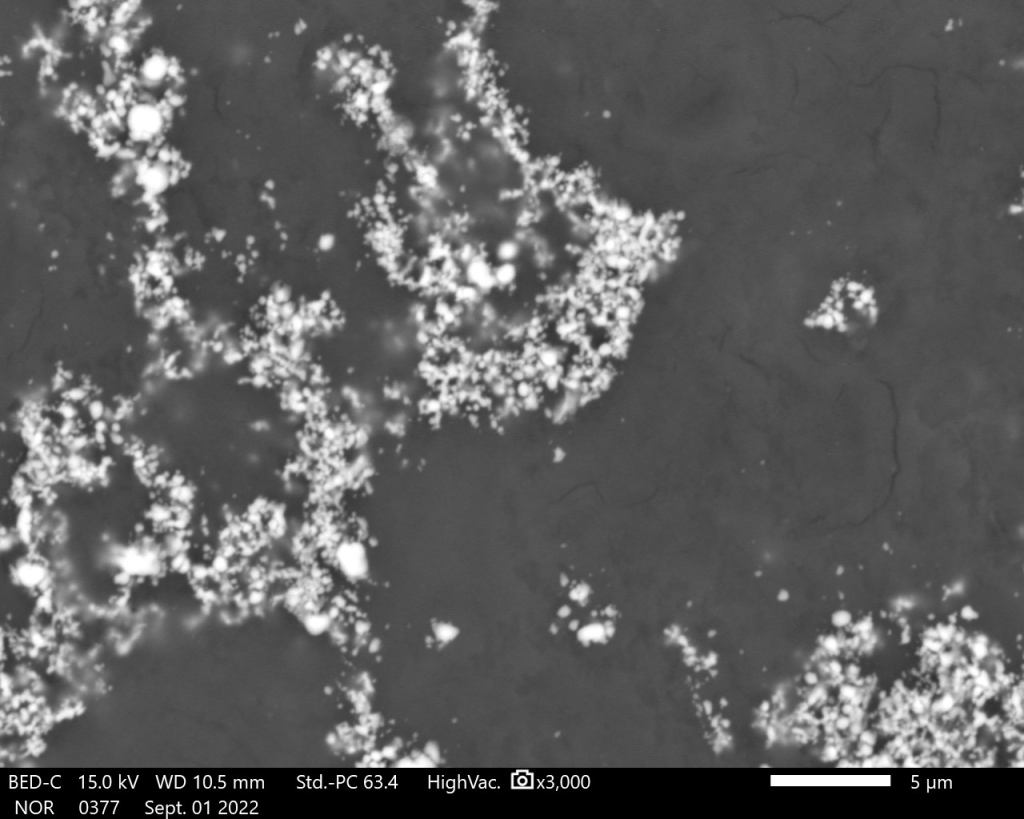
Figure 4 Mg-Zr20 master alloy Zr particle size distribution
3.Third-party test report